Process control optimization of rotary kiln line, raw mill ...
Process control optimization of rotary kiln line, raw mill and coal mill at the Adana cement plant in Turkey. ... Decrease in grinding cost; ... raw mill and coal mill were being operated by a PLC based central automation system in the plant.
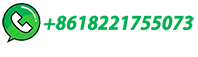