INVESTIGATION OF THE ELECTROCHEMICAL FACTORS …
and significance of grinding environment in mineral and ore flotation [8, 10-25] but these investigations are not reported for grinding of porphyry copper sulphide ores. Therefore, this paper was aimed to study electrochemical behavior inside ball mills and influence of milling environment (pulp chemistry) on flotation process.
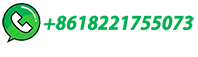