Grinding process - summaryplanet
Centerless Grinding. Centerless grinding is a high production process for continuously grinding surfaces in which the workpiece is supported not by centers or chucks, by a blade (figs. 16.1 a and b). Typical parts made by centerless grinding are roller bearings, piston pins, engine valves, camshafts, and similar components.
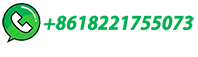