Disk Mill PULVERISETTE 13 classic line / Description ...
High final fineness for large quantities. The especially heavy and solid FRITSCH Disk Mill PULVERISETTE 13 classic line is the ideal instrument for fine grinding of up to 150 kg per hour of hard-brittle and medium-hard solids – even in continuous operation. The maximum feed size per piece is approximately 20 mm edge length, the final fineness is freely adjustable between 12 …
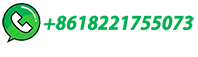