DESIGN AND ANALYSIS OF BALL MILL INLET CHUTE …
Ball mills (Fig 1.1) are coming in cement plant areas of raw grinding, coal grinding and cement grinding which in turn as raw mill, coal mill and cement mill. Ball mills are horizontal tube mills having single or two compartments for grinding, Balls as grinding media and driven by …
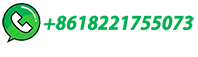