Cement Grinding Plant | Expert Cement Grinding Solutions ...
In addition to the cement mill, other commonly used equipment in the cement grinding station include cement mill separators, bag filters and ESPs, cement silos, conveyors, bucket elevators, cement roto packers, etc. How Does The Grinding Process Effect Cement Strength? The grinding system directly affects the quality of product cement.
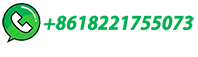