Heat And Mass Balance Calculations In Raymond Mill
Mass Balance Of Cement Mill Grinding Mill China in cement grinding section larfage cement ball mill heat balance heat balance calculator for cementexcel file BINQ MININg, heat balance cement ball mill performance sheet excel LA Machinery is a professional material processing designer and supplier in the world, we have excellen.
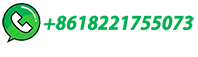