Siemens
Visit Siemens, the technology company focused on industry, infrastructure, transport, and healthcare.
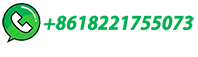
Visit Siemens, the technology company focused on industry, infrastructure, transport, and healthcare.
Cement Mill Department Free 3D model. This is a cement mill department. Having a separate building for the drive and compressors. Here the clinker, gypsum & pozzolona are measured in the hopper building and is fed into the cement mill. Here it is ground and the fine material is taken to the pump tank via the air slide and bucket elevator. .
Optimization of continuous ball mills used for finish-grinding of cement by varying the L/D ratio, ball charge filling ratio, ball size and residence time ... semi-finish-grinding plants have been used more and more for the energy efficient grinding of high-quality cement. In 1999, it was found that by decreasing the ball charge filling ratio ...
Monetary Benefits due to Process Improvements in Raw and Cement Mills Published on August 23, 2018 August 23, 2018 • 46 Likes • 5 Comments
Ball mills account for the majority of all mills in cement plants and therefore the optimization of established ball mills implies high savings potentials. Parameters that hold potential energy savings are load level, revolution speed, combination of the ball charge, lining design and the adjustments of the separator.
Cement is the glue that holds the concrete together, and is therefore critical for meeting society's needs of housing and basic infrastructure such as bridges … Ash Grove – Cement and Related Materials (Manufacturing Process)
Tokyo. Japan 1986 OPTIMIZATION OF CEMENT MANUFACTURING PROCESS G. Nakamura, T. Aizawa and K. Nakase Onoda Cement Co., Ltd., 1-1-7, Toyosu Koto-ku, Tokyo,japan Abstract. Cement manufacturing process is now operated with the aid of various control systems, such as raw meal compositi on control, kiln control and mill control.
Cement Ball Mill JXSC Machine. Cement grinding is the last process of cement production, it is to mix cement clinker and a small amount of gypsum, and then grind the mixture to a certain fineness, that is cement. You may also interest in the ball mill product price,lime ball mill,quartz ball mill . get price
ABSTRACT: The industrial sector represents roughly 22% of U.S. emissions. Unlike emissions from fossil-fueled power plants, the carbon footprint of the industrial sector represents a complex mixture of stationary combustion and process emissions produced as a reaction byproduct of cement, iron and steel, glass, and oil production.
properties. In the U.S., the different varieties of cement are denoted per the American Society for Testing and Materials (ASTM) Specification C-150. Cement is produced from raw materials such as limestone, chalk, shale, clay, and sand. These raw materials are quarried, crushed, finely ground, and blended to the correct chemical composition.
Mill Optimization with SICEMENT IT MCO. Cement production and, above all, cement milling, are highly energy-intensive processes. The cement mills are responsible for 45% of elec-tricity consumption. The use of expert systems offers a tremendous potential for savings. The expert system An expert system is a software system for process …
The optimization may also account for constraints on the process inputs and the process outputs. Finally, the first instance for each calculated future control signal is applied to the process. It is worth noting that normally the objective function is a weighted sum of deviations in the plant outputs and in the control signal increments.
The average salary for Business Process Optimization Manager at companies like U.S. CONCRETE, INC. in the United States is $129,256 as of November 29, 2021, but the salary range typically falls between $108,894 and $144,910.
Improved performance with advanced wear materials in vertical roller mills. 1 Wear pattern of the rollers. 2 Starting to rebuild 10 cm from the edge. 3 Maximum 20 mmwear after 15 000 hoursof service. 4 Rollers equipped with Xwin ® and neoX ® after 4010 running hours. 5 Original and wear profile. The cement market in India is continuously growing.
3BHS 211 545 ZAB E01/Rev A (07.06 500 Pomcany's) • stable coating in the kiln with stable raw meal fed to the kiln • formation of favourable clinker phases grown from raw meal with consistent properties • kiln optimization has fewer fluctuations to cope with • cement is ground to high quality from consistent clinker
Complete cement book bank, supper----excellent---mind blowing. Reviewer: MALAMBUGI - favorite favorite favorite favorite favorite - August 30, 2014 Subject: REUBEN . I LIKE IT . 59,139 Views . 6 Favorites. 2 Reviews . DOWNLOAD OPTIONS download 2 files . ABBYY GZ . …
HGT Gyratory Crusher. cement mill optimisation ppt . process optimization of cement grinding mill Process Diagnostic Studies for Cement Mill Optimization A 15 mio t/a cement plant is having a closed circuit ball mill for cement grinding: The mill has been The velocity of gases calculated through mill is 129 m/sec Contact Chat Online cement ball ...
Process Diagram Of Cement Mills. Process Diagram Of Cement Mills At the beginning of the 90s the mill in cement grinding and have new progress there the basic process of the roller mill is the final grinding but in order to fine powder with an air flow mill collected in …
PDF | On Sep 17, 2015, Smbat Mazmanyan published THE INCREASE OF THE SAS EFFECTIVENESS WHEN GRINDING PORTLAND CEMENT CLINKER OBTAINED FROM THE WASTE PROCESS OF SEMICOKING JAJOUR SHALE | Find, read ...
concrete, lignite particles near the surface can expand and cause the pop outs. Lignite is often referred to as brown coal, it is the lowest rank of coal quality. Item Mass % of Total Sample Clay lumps and friable particles 3.0 Material finer than 75 micron (No. 200) sieve: Concrete subject to abrasion 3.0* All other concrete 5.0*
the process according to key per-formance indicators (KPIs). While this might seem like a 'wish list', it is absolutely realistic. A closer look at how IIT is being instantiated in the cement industry shows why. From raw data to useful information To provide the most complete picture of a cement plant's performance, data from
process diagnostic studies for cement mill optimisation v.k … cement plant The benefits that can be achieved due to the optimisation of cement grinding … grinding mode • Vertical roller mill … cement grinding mills and 6 raw …
9780870449291 087044929X Lost Kingdoms of the Maya, Gene S. Stuart, George E. Stuart 9780828841061 0828841063 Linguaphone English Course for Italian Speakers - Beginner's Course, Linguaphone 9780809429202 0809429209 Dried Beans and Grains, Time-Life Books.
Cement slurry density can vary from 11 ppg to 18.5 ppg. The density is controlled by adjusting the amount of mix-water or additives. The cement slurry density is relatively higher than the density of drilling fluids which has to be considered when planning for cement job especially when formations with normal pore pressure trend.
The jet mill operates on the principle of collisions between particles to grind ultrafine powder material without the introduction of heat or any other external force and is capable of particle size reduction from about 100 microns down to 250 nm. The optimization process depends on parameters such as feed rate, grinding air pressure, physical characteristics of the solids …
Stage 4: Finish Process Cement Production. Greater Detail: Cement Plant Operations Handbook Crewmen''s Guide, Finish Mill Systems Cement mill A 10 MW cement mill, output 270 tonnes per hour A cement mill (or finish mill in North American usage[1]) is the equipment used to grind the hard, nodular clinker from the cement kiln into the fine grey powder that is cement.
The process stages are: 1. Milling. The bauxite is washed and crushed, reducing the particle size and increasing the available surface area for the digestion stage. Lime and "spent liquor" (caustic soda returned from the precipitation stage) are added at the mills to make a pumpable slurry. 2.
9781878901460 187890146X Robert Brewer's Captains (the Good, the Bad and the Ridiculous) - The Crewman's Guide for a Better Understanding of Your Captain's Moods, Methods & Madness, Robert Brewer 9781564405401 1564405400 Bradt - …
Cement production and above all cement milling are highly energyintensive processes the cement mills are responsible for 45 of electricity consumption the use of expert systems offers a tremendous potential for savings the expert system an expert system is a software system for process optimization.
It's primary objective is to achieve continuous process optimization and thereby improve the plant's overall performance. Hence its advantage as a graphical engineering and programming environment, used to control and optimize • Kilns • Mills • Alternative fuels with a combination of proven and advanced control techniques.
حقوق النشر © 2024.Artom كل الحقوق محفوظة.خريطة الموقع