Deagglomeration & Dispersing | Wet Milling Process
The wet milling process is a safe and efficient alternative to dry milling. Unlike dry milling, wet milling does not cause dust to form, so elaborate technical solutions, such as dust removal systems, inert gas purging, and dedicated containment are not necessary.
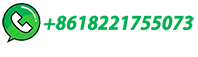