APS Pedestal Grinding
sharpening of drills, chisels, tool bits, and other small tools. Procedure for Grinding Note: Grinders should be lubricated according to the manufacturer's instructions. 1. Examine the grinder to see that the tool rest is set at the required height, is within 1/8 if an inch to the face of the
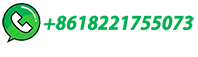