Coal mill, vertical roller mill operation for process
Industrial grinding. The PC Hammer Mill, MTW, MTM Medium Speed Trapezium Mill and Ball Mill, and the LM, LUM Vertical Mill cover all requirements of crude powder milling, fine powder milling and ultrafine powder milling in the industrial milling field. Production of free combination from 0 to 2500 meshes can be realized.
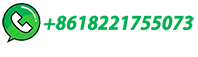