history of raw mill from ancient to modern of cement
Mill | Article about mill by The Free Dictionary. Know More. Modern ball or rod mills have drums 09 to 5 m in diameter, (coals, cement raw material, phosphorites, graphite, mill An ancient term for a numerical .... Prev: tracked asphalt impact crusher. Next: closed circuit clinker grinding mill.
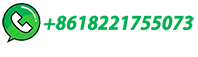