Analysis of Power Draw in Ball Mills by the Discrete ...
Abstract Ball mills, like other comminution devices, consume large amounts of energy. Mill operators often have to assess the power draft of mills for an entirely different set of operating conditions or for a reconfigured circuit. It is shown that the power draft can be accurately predicted from analysis of the motion of the charge. The motion of the charge is rigorously …
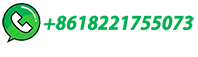