SRON Steel Silo For Cement Plant/Clinker Mill Plant/Power ...
HENAN SRON SILO ENGINEERING Co., Ltd. is China leading reputable EPC Contractor for bulk materials storage silo project, closed stock ground, and bulk materi...
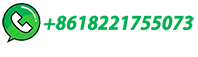
HENAN SRON SILO ENGINEERING Co., Ltd. is China leading reputable EPC Contractor for bulk materials storage silo project, closed stock ground, and bulk materi...
Operate at high mill temperatures (120-125°C), resulting in high gypsum dehydration and high cement temperatures that simulate ball mill cement and will be silo-safe. Operate at medium temperatures (80-120°C). If the plant does not experience problems, has short storage times and/or or the plant has special conditions for cooling the cement ...
Normally the single silo size at 5000-15000ton and total around 1000000ton. It uses sweep auger for grain discharging. All in all, the single silo size and amount is determined by the requirement of grain income and outcome needs. Above is only for reference.
GLOBAL CEMENT: PLC ENHANCEMENT 2 Global Cement Magazine June 2016 - Reprint usually regarded as beneficial, e.g. regarding work-ability. Nevertheless, above a certain limit the fine limestone has an excessive water adsorbtion and separate grinding (ball mill and mixing equipment) is favoured.4 The production of PLC with a Vertical Roller Mill
CEMENT MILL (I) PACKING AND DESPATCH . The White cement stored in silos is packed in bags in the packing house. Compressed air is used for the free flow of cement from the silo and the hopper located above the packing machine. Cement is conveyed from the silo to the packing machine hopper through screw conveyors and bucket elevator.
6 EuroMix Silo – Site Requirements 2. Silo Base Requirements 2.5 metre s 2.5 metres l Silo Diameter = 2.5m l Maximum Silo Height = 7.2m l Silo Barrel Height = 4.3m l Maximum Weight Filled = 40.0 Tonnes l Weight of Empty Silo = 2.2 Tonnes 0.3 metres 3 metres 3 metre s Foundation Design Data Customers are responsible for designing a suitable
Stave Silos. Marietta Silos has remained an industry leader in the construction of stave silos since we developed the technology in 1920. Concrete stave silos are constructed using precast concrete blocks, or staves, that interlock. Staves used for silo construction are typically 10" wide, 30" tall, and at least 2" thick.
20-40t/h ready-mixed mortar plant dealers. high quality 50m3/h concrete batching plant 60 ready mixed 20 40t/h dry mortar blending plant 20t/h ready mixed mortar plant chiness 15 20 ton/hour plant dry mortar mixing machine. how to get the ...
from 1000mmx1000mmx1500mm size to <=25mm while Line 2 Limestone/Shale ... are proportioned and ground in Cement mill (one Closed circuit ball mill ... (cement) is stored in cement silos ready for dispatch. 8 Cement packing and Dispatch . In this unit the finished product (cement) from the storage silo is transported and ...
CEMENT SILO and SILO EQUIPMENTS. ELKON Cement Silos are being manufactured in ELKON cement silo factory (ELKON-3) by means of fully automated welding robots in precise molds. All cement silos from 50 tons capacity to 500 tons capacity are manufactured as bolted type for easy and cost-effective transportation. VIEW.
In the above circuits, material is fed from hoppers to ball mill for reducing the size to microns. In closed circuit, micro particles are fed to classifier for segregation of desired material (based on its size) and rejected one is once again passed through ball mill.
Cement Milll Separator. Cement mill separator or cement separator is a type of equipment that was widely used in the cement grinding system and raw mill system of cement plants The function of the separator is to separate the fine sized particles from the coarse sized particles so as to avoid material condensation and over grinding in the mill and improve the milling system …
Steel Cement is building a UBE Vertical Roller Mill, Raw Material Storage and Handling Facility and a Finished Product Storage Silo to increase its ability to meet current and future demands. The purpose of this plant is to receive slag (which is a byproduct from hot rolling steel) via bulk cargo ships and process it into a valuable element ...
The latter is sent to the mill inlet for regrinding and the final product is stored in concrete silos. Step 6: Packing Cement extracted from silos is conveyed to the automatic electronic packers where it is packed in 50 kg bags and dispatched in trucks.
Putting your best fuel forward. Lars Jennissen, N+P Group, describes the latest developments in waste derived alternative fuels and raw materials, and outlines how cement producers could utilise them to achieve higher thermal substitution rates. During the course of 2021, N+P has been able to continue its ambitious growth and development plans ...
Cement manufacturing: components of a cement plant. This page and the linked pages below summarize the cement manufacturing process from the perspective of the individual components of a cement plant - the kiln, the cement mill etc.. For information on materials, including reactions in the kiln, see the ' Clinker ' pages.
silo Cement mill Cement silos / Packaging Figure 1: Cement plant. Mill inlet Mill discharge Ball filling 2. compartment Ball filling 1. compartment Drive Intermediate diaphragm Discharge diaphragm Figure 2: Ball mill. mill grinding circuits are very uncertain. Variations and het-erogeneities of the cement clinker feed a ects the gains, time
3750 cubic foot stainless steel silo plastic resin grain silo 3750CFSSsilo01. 3,750 cubic foot stainless steel silo for resin, plastic or powder measures 12'-0" in diameter X 40'-0" overall height. Cone is 79" deep or 48°. Silo was last used for plastic pellets and is currently located in ...
suijitupian71.jpg / cement mill ball mill data book for mechanical . vertical cement mill operational data ball mill for cement grinding The ball mill is designed for, cement mill is a corrugated, and information and data vertical cement mill stepwise process operation . cement mill technical data pdf files. cement mill technical data files.
Lumps and blockages in cement silos have long been an issue at some cement plants. In the 1970s, FL conducted research on ball mills and cement storage that revealed the cause to be an unfortunate combination of insufficient gypsum dehydration in the mill, high silo storage temperature and lengthy storage time.
Kiln Dia: 5.6 m X 82 m Capacity : 9,000 TPD 6 stage, 2 string PH In line calciner Clinker silo Capacity : 75,000 Tons Hot air to RP Hot air to Coal Mill Cement VRM Capacity : 175 TPH OPC 6000 T Slag 5000 Storage silo 16 X 1000 T 3 X 3000 T Cement EDM ...
Cement ball mill The cement ball mill is a horizontal cylindrical rotating device with outer gear transmission. The rotation of the cylinder produces a separation Heart force brings the steel ball to a certain height and then falls. Cement ball mill is used to grind cement raw materials, it is divided into dry method and wet method. Tubular ...
The latter is sent to the mill inlet for regrinding. The final product is stored in concrete silos as cement. Cement is so fine that 1 pound of cement contains 150 billion grains. 6. Final Product. The cement is now ready for transport to ready-mix concrete companies to be used in a variety of construction projects.
2500TPD new type dry process cement clinker production line. The 2500t / d cement clinker production line adopts a new dry process, with an annual output of 775,000 tons of cement clinker and a total cement output of 1.05 million tons / year. A cement production line and auxiliary facilities from limestone crushing to cement packaging are ...
Cement Mill Building, Mill Foundations, RCC hoppers, Silos, ... / Process water distribution based on system requirement and also developing required piping layouts including piping sizing. ... Cement silo supporting structure Empty bag godown Administration and all miscellaneous. Buildings and other services including roads & drainage
MG 60 To 300 Ton Bolted Detachable Cement Silo Bins is designed for cement, sand, fly ash, dry mortar, Ash calcium, lime stone powder etc of powder material or small size material storage, The silo equip level meter, it can display the location of the material and how much, arch braking device can remove material deposition caused by strong for too long.
White cement is a type of special cement, belongs to decoration cement.In general, Portland cement is greyish-green, as the name suggested, white cement is white. In the cement manufacturing process, in order to avoid the mixing of colored impurities, calcination of white cement plant mostly use natural gas or heavy oil as fuel.
With our cement industry and application knowledge, Malvern Panalytical instruments enable: Control of mill operation through analysis of composition and fineness of raw mill feed. Check of mill operation through quality control of raw meal. Check of composition and material balances (e.g. K, Na, S, Cl) through filter/ESP dust analysis.
In the cement mill the material is converted into fine powder. This is where cement is manufactured. The fineness of cement depends on the Blaine. The capacity of cement mill depends on the capacity of the plant such that if the capacity of the plant is 800 TPD then the capacity of the mill will be 800/20 = 40TPH.
Dosing Silos 6 x silos with various sizes, with weigh feeders Cement Mill 1 x 250 TPH Vertical Roller Mill Cement Storage 4 x 10,000 tons capacity Cement Packing and Dispatch 3 x 90 TPH Rotary Packing machine Water Source 2 Deepwell Pumps (capacity: 110 cu.m./day) Air Pollution Control Bag Filters Wastewater Pollution Control Septic Tanks
حقوق النشر © 2024.Artom كل الحقوق محفوظة.خريطة الموقع