Animal feed manufacturing process
Step 02: Feed Crushing Process The hammer mill is an important equipment for the raw material grinding process. The hammer mill can grind the ingredients into the desired size. Suitable for small and medium-sized feed making plants. If you have a large feed granulation factory, then the drop hammer mill is ideal. Step 03: Feed Mixing Process
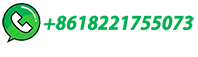