Wet Grinding - NETZSCH Grinding & Dispersing
The wetting and homogenization of solids in liquids, deagglomeration and dispersion, all the way to true comminution of primary particles make the agitator bead mill a universal wet processing machine. Depending on the product properties, various types of agitator bead mills with different grinding systems are employed. DeltaVita®
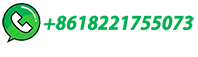