Grinding Machine: Types, Parts, Working & Operations (With ...
A grinding machine or grinder is an industrial power tool that uses an abrasive wheel for cutting or removing the m aterial. It is a process of metal cutting by using a rotating abrasive whee l from the surface of the workpiece. Generally, the grinding is finishing operation to show the high surface quality, accuracy of the shape and dimension.
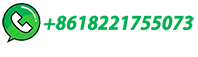