Ball Mill - SlideShare
We discuss the types of ball mill, the basic principles of the ball mill, how it works, the details of design including equations for optimum dimensions in all cases, some manufacturers for the ball mill, and estimation of the cost the ball mill. 6. 1. Introduction Ball mill is an efficient tool for grinding many materials into fine powder.
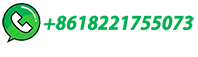