What is the key parameters in cement process ...
Cement mill process parameter list bvmbouwnl. cement mill process parameter list rccicoin Cement mill Wikipedia A cement mill is the equipment used to grind the hard, nodular clinker from the cement kiln into Heat generated in the grinding process parameters of ball mill in cement industry operating parameter for ball mill cement grinding The effect of feed particle …
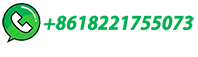