Ball Mill Parameter Selection – Power, Rotate Speed, Steel ...
The quality and surface area of forged steel balls of various sizes are shown in Table 1-12. A kind of Because of the wear of steel balls in the mill production process, in order to keep the mill stable. Steel balls need to be added regularly. The maximum diameter of additional steel balls is still determined by the method mentioned above.
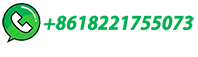