How Ball Mills Work (Engineering and Mining) - YouTube
Learn how a ball mill works, all of its main parts and some of its design features! This 3D animated video allows you to see all the internal parts of a ball...
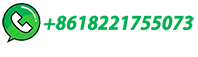
Learn how a ball mill works, all of its main parts and some of its design features! This 3D animated video allows you to see all the internal parts of a ball...
You can calculate the flow rate in five simple steps: Select the shape of the cross-section of the channel. Input all the measurements required to compute the cross-sectional area. Input the average velocity of the flow. Choose the unit of the flow rate. Click on the "Calculate" button to compute the flow rate. Liquid Flow Rate Calculator.
Mill Type Overview. Three types of mill design are common. The Overflow Discharge mill is best suited for fine grinding to 75 – 106 microns.; The Diaphram or Grate Discharge mill keeps coarse particles within the mill for additional grinding and typically used for grinds to 150 – 250 microns.; The Center-Periphery Discharge mill has feed reporting from both ends and the product …
How To Calculate Rpm Of Mill In Cement Plant. SAGMILLING Mill Critical Speed Determination The Critical Speed for a grinding mill is defined as the rotational speed where centrifugal forces equal N c is the critical speed. Get …
Tube mills 68 pg__Dimensioning of tube mills 69 pg__Tube mills 70 pg__Operation of tube mills 71 pg__Chap 8 Ball Mill grinding mill The Ball mill is a key equipment for regrindingBall mill is widely used in the field of cement the silicate product new type building materials fire-proof materials chemical fertilizer black and non-ferrous metal glass ceramics and etc...
What is the cutting power required for milling tool steel at a cutting speed of 80m/min. With depth of cut 2mm, cutting width 80mm, and table feed 280mm/min by Φ250 cutter with 12 inserts. Machine coefficient 80%. (Answer) First, calculate the spindle speed in order to obtain feed per tooth. n=1000vc÷πDC=(1000×80)÷(3.14×250)=101.91min-1
An International Company with Local Roots. Lehigh Cement Company began as a single-mill operation in Ormrod, Pennsylvania, in 1897. As the demand for concrete increased in the early twentieth century, the company thrived, making us a pillar of the many communities around us, bringing employment and economic benefit to small towns and big cities for more than 120 years.
https:// Learn about Ball Mill Critical Speed and its effect on inner charge movements. The effect of Ball Mill RPM s...
Adana cement plant in Turkey Process control optimization of rotary kiln line, raw mill and coal mill 20% decrease in standard deviation, 10% longer refractory life, 2.0% energy saving, 2.0% production increase
- Ball top size (bond formula): calculation of the top size grinding media (balls or cylpebs):-Modification of the Ball Charge: This calculator analyses the granulometry of the material inside the mill and proposes a modification of the ball charge in order to improve the mill efficiency:
The power rating also changes by the same ratio. To find the rim speed, which is usually shown as inches or feet per minute, multiply the diameter of the blade or cutter by PI (3.1416) and multiply that figure by the shaft RPM. 10 x 3.1416 = 31.416 x 5000 = approximately 155, 680 inches per minute.
History and geography of cement plants and kilns in Britain and Ireland. Cement Plants and Kilns in Britain and Ireland. About this site About cement About clinker List of plants Map of plants Raw materials About Kilns Other technical advances Trends in innovation Sources Historical Texts Reference Essays Contact Site Map. Picture of the firing ...
Critical speed graph. Example : A mill with 4.5 m dia (15′) N obtained = 20 rpm. If N = 15 rpm nc obtained = 75 %. Ball Mill Lining. The mill lining can be made of rubber or different types of steel (manganese or Ni-hard) with liner types according to the customers requirements.
1927 First Loesche coal mill delivered for the Klingenberg power station in Berlin. 1953 500th coal mill plant sold worldwide. 1961 Introduction of hydraulic spring assembly system. 1965 Construction of first pressure mill (LM 12.2 D). 1980 Delivery of first modular coal mill (LM 26.3 D). 1985 Delivery of first self-inerting coal grinding plant (LM 21.2 D) for the steel industry (PCI ...
It accounts for when the process is running slower than its theoretical top speed (both Small Stops and Slow Cycles). Formula: (Ideal Cycle Time × Total Count) / Run Time. Example:0.8611 (86.11%) Performance can also be calculated based on Ideal Run Rate. The equivalent Ideal Run Rate in our example is 60 parts per minute.
Performance Evaluation of Vertical Roller Mill in Cement Grinding Case Study ESCH Cement Plant Conference Paper PDF Available 183 September 2017 with 2 023 Reads How we measure reads ... Calculate and Select Ball Mill Ball Size for Optimum ... cement mill grinding media charge calculation calculate ball mill grinding media in cement YouTube ...
Quality Calculations. Most Frequently Used Calculators Now Available Online For Quality Evaluation and Process Control in Cement Industry. Lime Saturation Factor (LSF) Silica Modulus (SM) Alumina Modulus (AM) Hydraulic Modulus (HM) Silicic acid modulus (SAM) Total alkalies (as Na2O equivalent)
The cement industry is one of the most intensive energy consumers in the industrial sectors. The energy consumption represents 40% to 60% of production cost. Additionally, the cement industry contributes around 5% to 8% of all man-made CO 2 emissions. Physiochemical and thermochemical reactions involved in cement kilns are still not well understood because of …
It accounts for up to 40% of the total power consumption in mineral processing plant operations. So, selecting the efficient solution for grinding section is very important. Prominer provides ball mill / rod mill grinding system which is widely used in various types of ores' beneficiation, electricity, cement and chemical industries.
The critical speed of the mill, & c, is defined as the speed at which a single ball will just remain against the wall for a full cycle. At the top of the cycle =0 and Fc Fg (8.5) mp & 2 cDm 2 mpg (8.6) & c 2g Dm 1/2 (8.7) The critical speed is usually expressed in terms of the number of revolutions per second Nc & c 2 1 2 2g Dm 1/2 (2×9.81)1/2 ...
N = mill speed in RPM HP = A x B x C x L Where A = factor for diameter inside shell lining B = factor which includes effect of % loading and mill type C = factor for speed of mill L = length in feet of grinding chamber measured between head liners at shell- to-head junction
additive) are proportioned and ground in Cement mill (one Closed circuit ball mill in line 1 and two Roller press+closed circuit ball mill in line 2) based on the type of cement to be produced keeping the quality of cement equal or above the required standard. For instance (Clinker+Pozzolana+Gypsum) are proportioned and milled
installed 1969 in a cement milling process in the cement plant Le Havre in France. In the first few years, the GMD was only used in the cement industry. The GMD is also known as "wrap-around motor" or ... (Fig. 3.) with typical mill speed requirements of about 10 rpm for larger SAG mills and about 15 rpm for smaller ball mills. Figure 3.
The "Critical Speed" for a grinding mill is defined as the rotational speed where centrifugal forces equal gravitational forces at the mill shell's inside surface. This is the rotational speed where balls will not fall away from the mill's shell. Result #1: This mill would need to spin at RPM to be at critical speed. Result #2: This mill's ...
Raw Mill Optimization Module The Raw Mill Optimization option controls both the temperature, the feed rate to the mill and the separator speed in order to achieve the required throughput for kiln. Where starting the mill requires dampers to be moved, to change gas flow paths, the module will also respond to these effects to keep the system stable.
– Calculate roll separation force ("rolling force") and torque – Processing Limits – Calculate rolling power. Prof. Ramesh Singh, Notes by Dr. Singh/ Dr. Colton 13 Flat Rolling Analysis • Consider rolling of a flat plate in a 2-high rolling mill
Cutting generates a lot of heat, making oil based coolant preferable. Many machining spindles require 2000 rpm or more, to provide adequate cutting torque, which means that you have to use relatively small diameter end mills in order to end up with surface speeds this low. If not using coolant, then max surface speed is 50 ft/min. Insulation
8.3.2.2 Ball mills. The ball mill is a tumbling mill that uses steel balls as the grinding media. The length of the cylindrical shell is usually 1–1.5 times the shell diameter ( Figure 8.11). The feed can be dry, with less than 3% moisture to minimize ball …
these plants, sand, aggregate, cement and water are all gravity fed from the weight hopper into the mixer trucks. The concrete is mixed on the way to the site where the concrete is to be poured. At some of these plants, the concrete may also be manufactured in a central mix drum and transferred to a transport truck.
3.1 Introduction. The unit cost of logging or road construction is essentially derived by dividing cost by production. In its simplest case, if you rented a tractor with operator for $60 per hour - including all fuel and other costs - and you excavated 100 cubic meters per hour, your unit cost for excavation would be $0.60 per cubic meter.
حقوق النشر © 2024.Artom كل الحقوق محفوظة.خريطة الموقع