INCREASING THE USE OF ALTERNATIVE FUELS AT …
viii Increasing the Use of Alternative Fuels at Cement Plants: International Best Practice Cement is paramount for economic development and poverty reduction in emerging markets. Along with aggregates and water, cement is the key ingredient in the production of concrete, and, as such, is an essential construction material
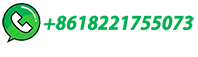