The Effect of Grinding Media on Mineral Breakage ...
According to the fractal analysis of the three sections of magnetite ground by steel balls of different diameters, the fractal dimension of the coarse and medium fine particles of ground magnetite products was between 2.00 and 3.00, and energy was consumed between the volume and the sur- face in the grinding process.
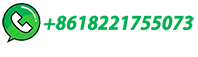