DESIGN AND ANALYSIS OF BALL MILL INLET CHUTE FOR …
a rotary kiln grinding the cement clinker nodules. Grinding occurs at the beginning and the end of the cement making process. Approximately 1.5tonnes of raw materials are required to produce 1ton of finished cement. The electrical energy consumed in the cement making process is in order of 110kWh/tonne and
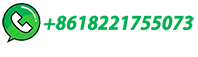