how we can increase our ball mill grinding capacity
Aug 18, 2019 Grinding process. For ball mills of the same specification, the closed circuit process yields 15-20% higher than the open circuit process. In the closed circuit operation, choosing the proper powder selection efficiency and cycle load rate is an important factor to increase the ball mill capacity. The effect of grinding aidget price
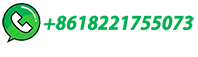