Crushing Plant Equipment | Fleet Of Crushing, Grinding And ...
Iron ore is a critical product for steel industry. The natural iron ore usually requires beneficiation, using techniques like milling, crushing, heavy media separation, silica froth flotation and screening to enhance the concentration of the ore and eliminate contaminants. As a result, you will get high quality fine ore powders, known as fines.
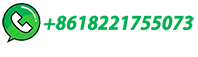