Comminution - an overview | ScienceDirect Topics
Semi-autogenous grinding mill. It is a rotating barrel in which ore is broken by ore pieces (0.2 m diameter) and steel balls (0.1–0.14 m diameter) falling on ore as they are lifted and fall off the moving circumference of the barrel. Autogenous grinding mills are similar but without the steel balls. The mills are fed and grind continuously.
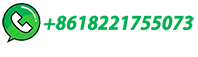