Common & Basic Formulas for Mineral Processing Calculations
To estimate the circulating load in and the efficiency of a classifier operating in closed circuit with a ball mill. Original feed may be applied at the ball mill or the classifier. T—Tons of original feed. X—Circulation factor. A—% of minus designated size in feed. B—% of minus designated size in overflow.
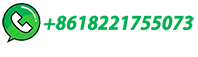