PHYSICOCHEMICAL PROBLEMS OF MINERAL PROCESSING
Accepted manuscript 2 The effect of ball size distribution on power draw, charge motion and breakage mechanism of tumbling ball mill by discrete element method (DEM) simulation
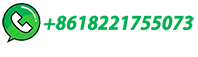
Accepted manuscript 2 The effect of ball size distribution on power draw, charge motion and breakage mechanism of tumbling ball mill by discrete element method (DEM) simulation
When the planetary mill is scaled-up in geometrical similarity, the impact energy of the balls is proportional to 4.87 power of the scale-up ratio. AB - The objective of this paper is to investigate the scale-up method of the planetary ball mill by the computational simulation based on Discrete Element Method.
Simulation Of Size Reduction In Ball Mills And Dem. The mill with 30 cm in diameter and 30 cm in length and the test conditions are standardized with a maximum ball size of 40 mm and an ore top size of 335 mm with less than 300 balls it poses no challenge in running the simulations if only grinding media are included for such a small mill one could also include the ore or powder …
A deeper understanding of the milling operation of ball mills helps mineral processing engineers to control and optimize them, and therefore, reduce their consuming power. In this work, the milling operation of ball mills is investigated using two methods, i.e. DEM and combined DEM-SPH. First, a pilot scale ball mill with no lifter is simulated by both methods.
Mishra BK, Rajamani RK (1992) The discrete element method for the simulation of ball mills. Appl Math Model 16:598–604. Article Google Scholar 17. Morrison R.D., Cleary P.W., 2004, Using DEM to model ore breakage within a pilot scale SAG mill, Minerals Engineering, Volume 17, Issues 11–12, Pages 1117–1124. 18.
obtained from the simulation of ball motion. This infor-mation is an important factor for controlling the changes in characteristics of the solid materials in the grinding process. Kano et al.8) found that it was the impact ener-gy of the balls that has a large effect on the grinding. Rocking mills (ball mills where the pot is rocked
Ball Mill Stirred Mills HPGR 20 – 5 5 – 0.2 0.2 – 0.001 20 – 1 7 5 1.5 ... • The present work shows that using DEM 2D simulation techniques it is possible ... which is directly related with mill power draw, internal motion of mill charge, optimal liner wear and throughput.
Changed ball mill to corner rad, now I'm stuck with a million stepovers Announcements The Autodesk Security Team is investigating the Log4Shell vulnerability (CVE-2021-44228) and (CVE-2021-45046).
wear, and power draw in a ball mills through DEM simulation. Several studies have been reported on modelling of mills by DEM simulations. For example, Xie et al. [6] studied the effect of filling level on the vibration and How to cite this paper: Mhadhbi, M. (2021) Simulation of a Laboratory Scale Ball Mill via Discrete Element Method Modelling.
Optimization of mill performance by using online ball and pulp measurements by B. Clermont* and B. de Haas* Synopsis Ball mills are usually the largest consumers of energy within a mineral concentrator. Comminution is responsible for 50% of the total mineral processing cost. In today's global markets, expanding mining groups are trying
The effect of ball size distribution on power draw, charge motion and breakage mechanism of tumbling ball mill by discrete element method (DEM) simulation Article Full-text available
Ball mill simulation. Separator simulation. DEM simulation. Grinding media wear rate. For monochamber mill. For 2 chambers mill. Payback, ROI and IRR. Mill's internals. Circuit modification. Mass balance. Open circuit. Filters sizing. Electroprecipitator. Grinding circuit cost. Grinding plant sizing. Closed circuit 1.
Inventor Cam, breaking edge with ball mill. I need to break an edge along a compound angles, basically along 2 chamfers intersect using a 1/8 ball mill. I have tried using trace, it follows the path in simulation but not with posted g-code, in the passes tab I use sideways compensation "left" but it does not add a G41 cutter comp, I attached ...
the primary crusher performance and proper control of the ratios for the SAG mill feeders drawing the ore from the stockpile. The ball mill grinding efficiency was poor and could be indicated by the fraction < 125 µm of only 5-9 % or x. P, 80: >400 µm in the mill discharge. This was deemed due
Ball Mill Simulator Crushing Equipment For Sale In South Ball mill simulation YouTube 8 Jul 2009 60 de la velocidad cr Vibrating BALL MILL SIMULATION CGM mining application VIBRATING BALL MILL, 3 CHAMBERS MEASURING 16 DIA.
In this research, the effect of ball size distribution on the mill power draw, charge motion regime and breakage mechanism in a laboratory ball mill was studied using the discrete element method (DEM) simulation. The mill shell and crushing balls were made of Plexiglas® and compressed glass, respectively. Modeling was performed using Particle Flow Code 3D (PFC3D).
Ball Mill Calculation Formulas Infinity For Cement Equipment. Mill Grinding Wikipedia. ... Simulation Of The Mineracao Serra Grande Industrial Grinding Circuit - May 17, 2019. Email This BlogThis! Share to Twitter Share to Facebook Share to Pinterest. Labels: ball mill design handbook pdf.
basis was a SABC circuit of 8% ball charge. Maximum SAG mill power was determined by deducting the installed ball mill pinion power of 7.95 kWh/t from the maximum overall circuit power of 16.7 kWh/t to give 8.75 kWh/t. Overall power for the comminution circuit (SAG plus ball mills) base on a
Hammer mills. These mills, which were original driven by water wheels, but later also by steam power, became increasingly common as tools became heavier over time and therefore more difficult to manufacture by hand.. The hammer mills smelted iron ore using charcoal in so-called bloomeries (Georgius Agricola 1556, Rennherden, Rennfeuer or Rennofen: from Rinnen = …
balll mill section drawing . ball mill section drawing ball mill in autocad drawing,Milling cutter, the free encyclopedia 1 Features of a milling cutter; 2 Typ 21 End mill; 22 Slot Mill; 23 Roughing end mill; 24 Ball nose, Ball Screw Conversion This is a picture from the bottom of the .Inserting P&ID Schematic Symbols AutoCAD Electrical,In
The results of this simulation is a function of mill size, ball charge volume, lifter profile and mill rotation speed. These relationships also allow the possibility of deter- mining the amount of energy consumed and distributed in the ball charge as a function of the variables men- …
In China, the largest ball mill of 7.9 m in diameter and 13.6 m in length was developed and applied successfully in a mine. It is also intensively recognized that the wave lifter profile is widely used for the ball mill. However, little …
This paper presents a dynamic simulator of the electromechanical coupling start-up of a ball mill. The electromechanical coupling model based on the dynamic model of the ball mill, the characteristic equation of the clutch, and the dynamic model of the induction motor is established. Comparison between the simulation results of angular speed, load torque and current …
secondary mill power that permits the range of vari- ability samples to be processed according to whether a "SAG Mill limiting" condition, i.e., harder ore, or a "Ball Mill limiting" condition, i.e., softer ore exists. For example, a ratio of 1:1.5 or up to 1:2 would indicate a trend away from processing harder ore types and
ball mill at Mintek. This mill was designed and built for grinding of PGMs. It measured 0.4 m in diameter and had four independent sections of 0.2 m each. It was fitted with 12 lifters spaced circumferentially around the mill shell. It also allowed the use of variable lifter face angles along the mill axial length. DEM simulation parameters
A major advance in the modeling of ball mills became possible through the development of the discrete element method. DEM provides a numerical procedure for solving Newton's second law with an appropriate contact relationship that can be applied to describe the motion of each grinding medium contained in the mill charge to predict element position, velocity and forces …
The power draw for the simulated ball mill (5700 kW) is close to its rated motor power (6000 kW), however, greater than the power draw for the actual mill (5268 kW). The increase in power draw is due to an increase in ball volume from 24% v / …
Using the Herz-Mindlin model, seen in the sun wheel reference frame. 108 steel balls.
for a particular input and output of a ball mill. The variables for the ball mill include the ball density (in gm/cm3), ball diameter (in meter), belly length (in meter), mill diameter (in meter), volume of balls (in %), and rotation speed (in RPM). After making all the changes, the user has to save them by clicking on the "Save" button.
Simulation Of Industrial Sag Mill Charge Motion In 3D Space … for "Simulation Of Industrial Sag Mill Charge Motion In 3D … This simulation of SAG mill keeps track of all the moving bodies like ball and rock and observes its …
حقوق النشر © 2024.Artom كل الحقوق محفوظة.خريطة الموقع