Operations and maintenance training for ball mills
Ball mills operations and maintenance seminar. Learn how to optimise your ball mill systems in this 5-day training seminar focused on best practices for operations and maintenance (preventive and reactive) to achieve energy savings, reduced maintenance costs and overall improved productivity of the ball mill systems.
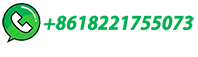