OUTLINE SPECIFICATION - United States Army
Mixture Proportions; The results of trial mixture design studies along with a statement giving the maximum nominal coarse aggregate size and the proportions of ingredients that will be used in the manufacture of each strength or class of concrete, at least 14 days prior to commencing concrete placing operations.
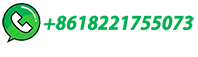