Solved: Inventor Cam, breaking edge with ball mill ...
Inventor Cam, breaking edge with ball mill. I need to break an edge along a compound angles, basically along 2 chamfers intersect using a 1/8 ball mill. I have tried using trace, it follows the path in simulation but not with posted g-code, in the passes tab I use sideways compensation "left" but it does not add a G41 cutter comp, I attached ...
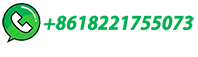