INSTRUCTION MANUAL FOR PRECISION ... - Kent Industrial …
(16).During grinding and before the grinding wheel stops rotating after work is finished,do not attempt to clean the shavings of the work piece or to move the workpiece. (17).When tak ing off the grinding wheel,use a flange remover to detach it.Do not use any method that involves pounding the grinding wheel.This could result in damage to the
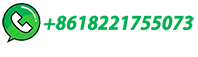