ISCAR Cutting Tools - Metal Working Tools - Precision ...
ISCAR is a dynamic full line supplier of precision carbide metal working tools, producing a wide range of carbide inserts, carbide end mills and cutting tools …
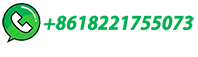
ISCAR is a dynamic full line supplier of precision carbide metal working tools, producing a wide range of carbide inserts, carbide end mills and cutting tools …
HSS is used for general purpose milling of both ferrous and non- ferrous materials. While usually inexpensive, HSS does not offer the tool life or speed advantages of cobalt and carbide end mills. Cobalt: Cobalt is an M42 tool steel with an 8% cobalt content. Cobalt is more expensive but provides better wear resistance and toughness than HSS (M7).
An aluminum block of length 50 mm and width 70 mm is being milled using a slab milling cutter with 50 mm diameter. The feed of the table is 15 mm/min. The milling cutter rotates at 60 RPM in clockwise direction and width of cut is equal to the width of the workpiece. Draw a neat sketchof the milling operation describing aboveconditions. The
Best Metal Lathe Mill Combo In December 2021. It is not an easy task to choose the Best Metal Lathe Mill Combo if you aren't a frequent buyer. But don't worry – we have compiled here the perfect list of Top 10 Best Metal Lathe Mill Combo for you. Have a look at our list and choose the ones you like the most.
This is a heavy-duty, biostable, semisynthetic fluid with chlorinated EP additives. It allows for a long sump life and can be used in a wide range of operations, from milling to drilling. Houghton Hocut 795B. Order Now Mobil Mobilcut 100 Aqueous Metalworking Fluids. Order Now
CNC Milling machines • The primary function of a CNC Milling Machine is that your tool will be doing the rotating and moving while your workpiece stays in one spot (generally). • Milling is a more specific process that is similar to drilling and cutting. • These machines can also be either horizontal or vertical, again
An example would be an 8-inch-diameter cutter, D c = 8 One pass milling to a depth of 0.7-inch tooth space, A e = 0.7 Thus, f z, modification factor = 5.7143 / 3.229 = 1.769 Therefore, if H ex of 0.008 is needed, then f z of 0.008 x 1.769 = …
Metal Slitting Saw Milling Cutter The metal slitting saw milling cutter is essentially a very thin plain milling cutter. It is ground slightly thinner toward the center to provide side clearance. These cutters are used for cutoff operations and for milling deep, narrow slots, and are made in widths from 1/32 to 3/16 inch.
JET | Milling Machines for Metalworking. JET Milling machines and components are manufactured for precision, reliability and durability. Table sizes ranging from 8" x 36" to 12"x 54" and drivetrains of step pulley, variable speed, and electronic variable speed allow for easy mill selection. Include installed accessories such as ...
• A milling machine removes metal by rotating a multi-toothed cutter that is fed into the moving workpiece. The spindle can be fed up and down with a quill feed lever on the head. • The bed can also by fed in the x, y, and z axes manually.
Abrasive suppliers offer a wide array of products for a wide array of grinding applications in metalworking. Choosing the wrong product can cost the shop time and money. This article presents some of the fundamentals of selecting the best grinding wheel for the job. Abrasives—Grits and Grains
Milling machines can be dangerous if not used properly. Read the owner's manual carefully. Make sure you understand instructions and are properly trained before operating a milling machine. Refer to Metalworking Machines - General for basic safety tips.
Milling is the machining process in which the removal of metal takes place due to the cutting action of a rotating milling cutter.In a milling machine, the cutter is rotating due to workpiece is fed against it.This machine can hold more than one tool at a time. The cutter rotates at high speed, and because of the many cutting edges, it removes metal at a very fast rate.
Speeds and feeds are the cutting variables used in every milling operation and vary for each tool based on cutter diameter, operation, material, etc. Understanding the right speeds and feeds for your tool and operation before you start machining is critical. It is first necessary to define each of these factors.
During rough machining, the workpiece has a great impact on the lathe tool. When taking λS ≤ 0°in finishing machining, the impact force of the workpiece on the lathe tool is small; when taking λ S ≥ 0°, λS=0°is usually taken. The inclination angle is generally selected between -10°and 5°. Sharing is caring! Keep In Touch.
TOOL MATERIAL SELECTION We use only the finest materials available to meet our customers demanding range of applications. Our stock includes high speed steel (M-2, M-4, M-7, M-42), powdered metal (PM M-4, PM M-48, PM T-15), & carbide (sub-micron grain, ultra-fine) in varying concentrations.
End milling - An end mill makes either peripheral or slot cuts, determined by the step-over distance, across the workpiece in order to machine a specified feature, such as a profile, slot, pocket, or even a complex surface contour.The depth of the feature may be machined in a single pass or may be reached by machining at a smaller axial depth of cut and making multiple passes.
Driva Anchor x3 Self Drill Metal Plasterboard Fixing With Pan Head Screw. 20x WRD SWIV Scaffolding Scaffold Fittings Swivel Couplers Clamps FREE DELIVERY, Roland Cutter Plotter Blades for Sign Making Machines Self Adhesive Vinyl Cutter, Mild Steel Box Section/Square Hollow SectionLARGE SELECTION38 SIZES. FLAT PACK FURNITURE FITTING SPEAKER ...
Metalworking Tools. Kennametal metalworking tools and tooling systems are the easiest and most convenient way to get your job done right. Our high-performance First Choice milling and drilling tools are versatile, working effectively on most of your machining applications. If the realities of your business require custom metalworking tools, we ...
Factors that must be considered when selecting milling tools include the type of material being machined, the shapes of internal and external profiles, the amount of stock to be removed along internal and external profiles, the desired finish of the part surfaces, and the capabilities of the machine. Audience
8.3.2.2 Ball mills. The ball mill is a tumbling mill that uses steel balls as the grinding media. The length of the cylindrical shell is usually 1–1.5 times the shell diameter ( Figure 8.11). The feed can be dry, with less than 3% moisture to minimize ball …
End Mill Flutes - What Are They, and How Many Do I need? The Spiral-shaped cutting edges on the side of the end mill are called flutes. Flutes provide an empty path for the cutting chips to escape from when the end mill is rotating in a workpiece. End Mills have either 2, 3 or 4 flutes per bit. 2 and 4 flutes are the most popular.
3. Milling • Milling – A machine operation in which a work part is fed past a rotating cylindrical tool with multiple edges. (milling machine) • Types – Peripheral milling • Slab, slotting, side and straddle milling • Up Milling (Conventional) & down milling (Climb) – Facing milling • Conventional face, Partial face, End ...
Typically, people are programming this operation using CAM software. Helical interpolation is one of the most reliable holemaking processes in the market, and with proper tool and parameter selection, it's an excellent weapon to have in your arsenal," said Jeremy Corneil, milling product manager for Iscar Tools Canada.
A conventional milling machine, also called a manual milling machine, is a machine that can manufacture all kinds of parts. The table feed is manually controlled by an operator. This kind of milling machine is particularly useful if you need a machine tool for unit production, small series production or reworking parts. They are very economical […]
Shop machines you can trust and quality industrial machine tools, known as fabrication equipment, and metalworking machinery. GMC Machine Tools is a proud manufacturer of fabrication and metalworking machinery located in the city of Ontario California; selling machine shop equipment and quality machine tools. We offer a wide selection of industrial machinery …
Metal Cutting Metal cutting involves removing metal through machining operations. Machining traditionally takes place on lathes, drill presses, and milling machines with the use of various cutting tools. Successful machining also requires knowledge about the material you are cutting. These classes will explain all aspects of metal cutting.
Introduction to Selecting Milling Tools IImportant decisions for the selection of cutting tools for standard milling operations The variety of shapes and materials machined on modern milling machines makes it impera-tive for machine operators to understand the decision-making process for selecting suitable cutting tools for each job.
CNC Milling Machine Spindle [Complete DIY Guide] [ CNC Milling Machine Parts Home] The cnc spindle is the heart of any mill. It consists of a rotating assembly with a taper where tool holders may be installed. A cnc spindle motor with optional transmission of …
Slot milling operation can use any type of milling cutter like plain milling cutter, metal slitting saw, or side milling cutter. Selection of a cutter depends upon type and size of slot or groove to be produced. Keyway Milling Operation. 12) Gear cutting milling.
حقوق النشر © 2024.Artom كل الحقوق محفوظة.خريطة الموقع