Co Mill, Conical mill, Comill, Cone Mill: Pharmaceutical ...
Size reduction also improves the powder's flow, bulk density, and compactness; 1.1 Co mill: size reduction in the pharmaceutical Industry . There are several techniques available for powder processing. In brief, we have crushing, milling, grinding, cutting, chopping, and micronizing. Each of these processes is carried out by different machines.
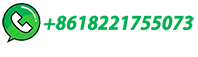