PILOT PLANT SCALE- UP TECHNIQUE
3.3. Standard pilot-plant equipment floor space: Discreet pilot plant space, where the equipment needed for manufacturing all types of dosage form is located. Intermediate ± sized and full scale production equipment is essential in evaluating the effects of …
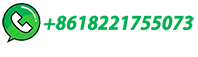