Ball Mill for Cement Grinding Process
Cement Ball Mill Structure. When Ball Mill is working, raw material enters the mill cylinder through the hollow shaft of the feed. The inside of the cylinder is filled with grinding media of various diameters (steel balls, steel segments, etc.); when the cylinder rotates around the horizontal axis at a certain speed, Under the action of centrifugal force and friction force, the …
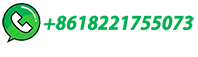