IMPROVING THERMAL AND ELECTRIC ENERGY …
2.5.2 Replacing a Ball Mill with a Vertical Roller Mill, High-Pressure Grinding Rolls, ... Figure 8: Fixed Static Inlet Section for a Clinker Cooler ..... 22 Figure 9: Optimized Cooling Air ... Table 1: Specific Thermal Energy Consumption by Rotary Kiln Type ..... 4 Table 2: Production Gains ...
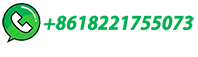