Flexible milling and grinding solutions that last | FL
Milling and grinding of raw material, minerals and cement is a rough process, with highly abrasive and hard feed materials that can accelerate equipment wear and tear. ... It is also adaptable to three different types of grinding setups: pre-grinding, semi-finish grinding and finish grinding. The OKTM mill can skilfully grind raw or cement feed ...
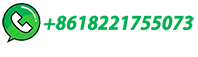