Ceramic Ball Mill For Grinding Materials - FTM Machinery
Ceramic ball mill is mainly used in material mixing, grinding. Henan Fote Heavy Machinery Co., Ltd has two kinds of grinding ceramic ball mill, one is dry grinding ceramic ball mill, and another is wet grinding ceramic ball mill. The machine can use different liner types according to different production needs.
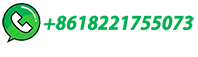