Handbook of Electric Machines - Infineon Technologies
Ball Rings: Bearings between frame and rotor shaft. Figure 4: Squirrel-cage rotor for induction machine (3) Figure 5: Cross section of a squirrel cage rotor with drop shaped bars (4) Motor Handbook 9 Structure and functional description Figure 1 shows the assembled arrangement of the stator and the rotor. ...
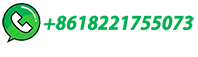