Hammer Mill: components, operating principles, types, uses ...
Hammer mill is the most widely used grinding mill and among the oldest. Hammer mills consist of a series of hammers (usually four or more) hinged on a central shaft and enclosed within a rigid metal case. It produces size …
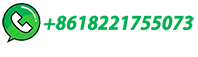