grinding ball | Magotteaux
Maxicrom® grinding ball. You can grind to the maximum with Maxicrom® grinder ball. It revolutionizes coarse grinding. It is used in the first chamber of raw grinding mills and cement tube mills. It leads the way in process efficiency and wears well with little deformation. Fewer top-ups will be needed which makes for less safety risks for ...
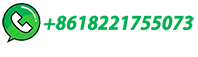