VALIDATION OF A CLOSED CIRCUIT BALL MILL MODEL Alex ...
Minerals processing engineers and grinding experts agree that classification efficiency and circulating load both have a major effect on the efficiency of closed circuit ball mills. However, the effect of each is difficult to quantify in practice as these two parameters are usually interrelated. Experimental work was undertaken by Process
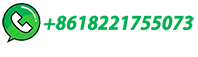