Roller Mills vs Hammer Mills - Which Is Best? | Automatic ...
A roller mill can efficiently break down grain for livestock feed. Energy efficiency is especially pronounced in electric grain roller mills.In some situations, roller mills use 85% less energy to process grain than hammer mills. In the most common processing situations, though, the energy savings are likely 30-50%.
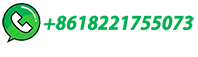