A new in-process material removal rate monitoring approach ...
The grinding process is conducted with a mean particle size of 75 μm, belt velocity of 32 m/s, and the workpiece feed rate of 4 mm/s. The material removal rates are 0.05, 0.082, 0.16, and 0.22 g/ (mm/s), respectively. Table 4 shows the feature values corresponding to the four spark field images.
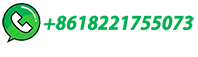