Cement Manufacturing Process, Cement Bricks Factory ...
Cement Grinding In the final manufacturing stage, gypsum is measured and added to the clinker in order to yeild the final product. After first passing the mixture through a roller press, it is further reduced into a fine powder with the help of a single chamber ball mill.
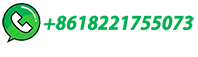