Bond Index Ball Mill / Rod Mill BT 100 XL - RETSCH
94 x 0.61" balls. The optimum number of grinding balls is 285. However, the ball diameters vary due to wear. Therefore, the total ball number should be adjusted from time to time to ensure a total mass of 20.125 grams. The grinding jar of the Bond Index Ball Mill measures 12″ x 12″ and has well-rounded corners. Module Rod Mill.
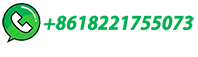