Steel Slag Vertical Mill - greatwallcorporation
The plant uses advanced vertical roller mill to grind the steel slag. The product steel slag powder is mixed into cement or concrete as a mixture, to significantly improve its strength, impermeability and frost resistance. The steel slag powder produced by the plant is sold well in cement plants and concrete mixing stations around Xuzhou, and ...
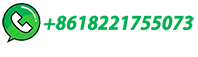