(PDF) Planetary Ball Mill Process in Aspect of Milling Energy
155. Planetary Ball Mill Process in Aspect of Milling Energy. Huynh Xuan Khoa, Sunwoo Bae, Sangwon Bae, Byeong-woo Kim. a., and Ji Soon Kim *. …
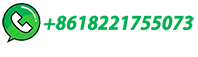
155. Planetary Ball Mill Process in Aspect of Milling Energy. Huynh Xuan Khoa, Sunwoo Bae, Sangwon Bae, Byeong-woo Kim. a., and Ji Soon Kim *. …
We provide ball mill machine for cement plant, power plant, mining industry, metallurgy industry, etc. Ball mill machine can grind a wide range of materials, with enough continuous production capacity, simple maintenance. Capacity range from 5t/h to 210t/h. The feeding size is less than or equal to 30mm. Learn more.
Tube mill. Tube mills consist of revolving cylinders, with a number of hard balls which act as the grinding media. Tube mills differ from ball mills essentially in having an inlet for material feed and an outlet for the ground material. Hence, tube mills have larger length to diameter ratio (≈3:1) as compared to ball mills (≈1.5:1).
The manufacture and preparation of charge powders are the first and one of the most important stages of producing composite materials by powder metallurgy [].Processing in planetary ball mills is often used to synthesize composite powders [].The main parameters that characterize the efficiency of planetary mill processing are the input energy (fraction of the …
This production level attritor stirred ball mill is designed for crushing and breaking down the primary particle size of materials. The high speed rotating axis and grinding media can crush, grind and shear the materials into granularity powder. It is widely used in pharmaceutical, mining, food, chemical, metallurgy and electronics research and ...
A ball mill consists essentially of a conical or cylindrical shell supported on hollow trunnion bearings on which it revolves ; the construction of the various types is described later. The ore enters through one trunnion and leaves by the other.
DECO offers bulk all lab planetary ball mills for sale with cheap price. We're known as one of the most professional all lab planetary ball mills manufacturers and suppliers in China, with the business principle of 'Customer is Superior, Quality is in the First Position Forever'.
Steel-Head Ball-Rod Mills are available in any one of five different types of discharge: Overflow, perforated overflow, return spiral, grate, and peripheral. To best serve your needs, the Trunnion can be furnished with small (standard), medium, or large diameter opening for each type of discharge.
Technical Advantages of ball mill: Gongyi Hengchang Metallurgical Building Material Equipments Plant is professional manufacturer of ball mill, and complete beneficiation plant for mineral ore. We provide flow chart free design service, can design 50-2000 ton/day turnkey project for mineral ore beneficiation. Features of ball mill: (1).
Rotary ball mill is composed of feeding part, discharging part, turning part, transmission part (reducer, small transmission gear, motor, electric control) and other main parts. The hollow shaft of the rotary ball mill is made of cast steel, and the lining can be removed and replaced. The large rotary gear is processed by casting hobbing, and the cylinder body is equipped with a …
example by impacts within a vibratory ball mill. The technique has a long history with significant contributions from Ostwald, Carey Lea and, notably, Faraday. Mechanochemistry has subsequently seen application in a variety of areas of materials science including mechanical alloying in metallurgy, the synthesis of complex organic molecules and ...
Planetary ball mill is a necessary device for mixing, fine grinding, small samples prepared, dispersion of nano material, R&D of new product and small batch production for high tech material. High-end vertical planetary ball mill
Tumbling mills Ball mill, Pebble mill, Rod mill, Autogenous / Semi autogenous mills. Tube mill. 89 84. 90 85. 91 A BALL MILL 86. 92 BALLS INSIDE A BALL MILL Balls range in size from 1-6 ". They are made of cast iron, forged steel or alloy steel. Larger balls help in coarse grinding . 87. 93 BALL MILLS ( 1876) .
A high-energy mill was designed and built with the purpose of processing magnesium (Mg) powders. The main characteristics of the mill are grinding capacity of 1 kg and demolition elements of 10 kg; it has a distributed form to the interior ten blades of similar geometry, six of which are of the same size and four of them were increased in length in order …
Planetary ball mills. A planetary ball mill consists of at least one grinding jar, which is arranged eccentrically on a so-called sun wheel. The direction of movement of the sun wheel is opposite to that of the grinding jars according to a fixed ratio. The grinding balls in the grinding jars are subjected to superimposed rotational movements.
Hydro & Electro Metallurgy Financial Engineering or Any HM/OC course 03 03 3-0-0 3-0-0 DE HM/OC Total Credits 22 VII Semester B.Tech. (MME) Course Code Course Title Credits L-T-P Category MML 471 Structural Metallurgy 03 3-0-0 DC MMP 471 Structural Metallurgy Lab. 01 0-0-2 DC MML 472 Environmental Degradation of Metallic Materials
Working principle of ball mill 1. This ball mill is horizontal type and tubular running device, has two warehouses. Notes for ordering of ball mill 1. While placing your order, please specify the model, quantity, and the rotating direction as well. 2. Since the ball mills are classified into two types: grate ball mill and overflow ball mill ...
Prof. Dr. M. Sherif El-Eskandarany, in Mechanical Alloying (Third Edition), 2020 Abstract. As was pointed out in the last two chapters, powder-milling process, using ball or rod mills, aims to produce a high-quality end product that can be composites and nanocomposites, and nanocrystalline powder particles of intermetallic compounds, amorphous, hydrides, nitrides, …
8.3.2.2 Ball mills. The ball mill is a tumbling mill that uses steel balls as the grinding media. The length of the cylindrical shell is usually 1–1.5 times the shell diameter (Figure 8.11 ). The feed can be dry, with less than 3% moisture to minimize ball …
The ball to charge ratio may be 5:1, 10:1, 15:1. This method is more efficient in achieving fine particle size. Rod mills: Horizontal rods are used instead of balls to grind. Granularity of the discharge material is 40-10 mm. The mill speed varies from 12 to 30 rpm. Planetary mill: High energy mill widely used for producing metal, alloy, and ...
Jaw Crusher technology. RETSCH Jaw Crushers are robust and powerful forced-feed crushers. The feed material passes through the no-rebound hopper and enters the crushing chamber. Size reduction takes place in the wedgeshaped area between the fixed crushing arm and one moved by an eccentric drive shaft. The elliptical motion crushes the sample ...
by two routes, namely Powder metallurgy and Casting method. The powder metallurgy route mainly consists of three stages, Mixing of the powders, compaction and sintering. The mixing can be achieved by many methods and one of such method is by …
Abstract. Ball milling has been used to produce fine particles from a coarse feed for an extended period of time. Traditional powder metallurgy uses various types of ball mills to produce fine material powders by the pulverization of the starting materials.
Disk Mills are suitable for fine grinding of medium particle sizes of soft to hard, brittle and temperature-sensitive solids. The material to be ground is comminuted by pressure and shearing action between two counteracting grinding disks with coarse interlocking teeth.
Ball mills are commonly used in the grinding stages of mineral processing. Application of Ball Mill Ball Mill is the cylindrical device used in grinding materials after the crushing process. 2. It retains the old ball mill end cover structure form, and uses large diameter inlet and outlet, therefore it has large processing quantity.
The milling was realized using a planetary ball mill for 10, 30 and 50 hours in an inert argon atmosphere at 300 rpm. Results shown in laser diffraction indicate a great reduction in the particle sizes of powders when VC is used. For 30 hours milling, D50 values ranged from 1580 µm with NbC to 182.3 µm with VC addition.
Laboratory flotation machine is mainly used in the laboratory of geology, metallurgy, gold, building materials, coal, chemical, mine, ore dressing laboratory and scientific research units, colleges and universities ore dressing teaching and research, used for stirring, cleaning, separation and selection of a small amount of ore samples. ZJH Minerals laboratory flotation …
A ball mill is a grinder which is used to grind, blend and mix materials like chemicals, ores, pyrotechnics, paints, mineral dressing process, paint and ceramic raw materials. Its working principle is impact and attrition. Ball milling have proved to be effective in increasing solid-state chemical reactivity and production of amorphous materials.
Rod & Ball Mills 3-6m 2.5 cm 2-4.5m 2-5.5m. 0.5 cm. 0.5 cm. 2-5.5m. 0.1. cm. 42 Rod & Ball Mills. Grinding Action. 43 Rod & Ball Mills. Media Filling: About 40%. 44 Brekage Mechanism. Mechanism: Impact, Nipping and Friction. 45 Tumbling Motion. 46 How to control product size To. control the product size from crushing, size classification is ...
Higher capacity per unit mill volume Makes possible the use of wet screening or classification for close product control Elimination of the dust problem Makes possible use of simple handling and transport methods such as pump, pipe, and launder Sampling Sampling definition :is the mean where by a small amount of
حقوق النشر © 2024.Artom كل الحقوق محفوظة.خريطة الموقع